This week I had a great sit-down chat with a friend who runs a design and manufacturing business. His company makes a combination of bespoke products and bespoke combinations of standard parts.
Whilst talking, the subject moved to how the company produces custom Bill of Materials (BOMs) for the designs they create. I thought it was a great subject to share.
Using two Sovelia products we can change the focus, benefit, and value of the creation of the BOM but still give the same(ish) result. Ultimately in this case, it's a list of what parts are needed to purchase, cut, check out of stores, assemble, deliver and the cost for the project.
Method today.
The company uses Autodesk Inventor, and a designer creates a model and drawings to a specification from the customer. Currently each design goes through the designer to create the drawings and BOM which is then printed and distributed.
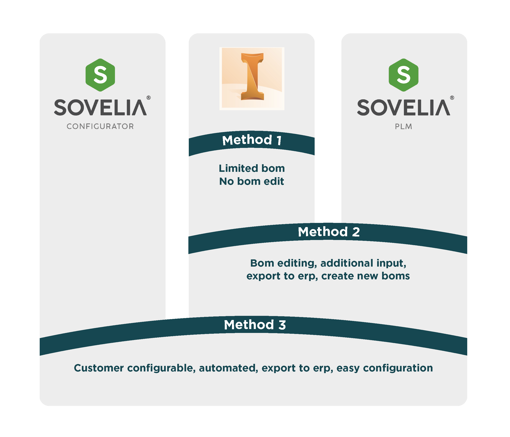
Alternative Method 1.
As many of the elements in the design are standard and used repeatedly the designer could start utilizing iLogic, an automation tool inside Inventor. iLogic would allow parameterization of the design and modularization of the process with Logic thrown in for good measure.
Benefit:
Reduced time for each design, repeatability of the design process, better quality of design with the reduction of errors.
Drawbacks:
It is still the designer who must do all these tasks and the bottle neck in the system. The BOM that comes out of Inventor may not be complete as it reflects the CAD model and nothing else. Others in the organization still get informed by a paper trail (not good for sustainability).
Alternative Method 2.
If the design department chose to send the standard model and drawing information to Sovelia Core PLM system, not only CAD but other information could be included in the BOM producing an enriched fully defined BOM. With access to the information in Sovelia Core others in the organization could assemble standard BOMs together to make new combinations of products leaving the designer free to concentrate on purely bespoke designs.
Benefit:
Capturing the BOM for the rest of the organization to see. Manipulation and creation of new BOMs by other members of the organization. Inclusion of additional non-CAD information in the BOM. Designer freed up to work on adding value. One source of the truth.
Drawbacks:
It may still be the designer that has to approve the final design. The CAD information must be sent to Sovelia Core PLM system.
Sovelia Blog: Bill of Materials (BOM) management at the heart of Sovelia Core
Alternative Method 3.
Let the customers design their own product. Using Sovelia Configurator standard combinations of the product can be defined. Through the web interface customers could then create the design they want from the standard combination available.
Benefits:
Design & sales are freed up to do other value-added tasks. Feedback to users can be much quicker and the process reach a conclusion faster. Logic can be included in the configurator designs meaning customers cannot design something you cannot make. Orders are generated in a standard format meaning no surprises.
Drawbacks:
Customer must have a level of knowledge about the product they are configuring. Standard Configurations must be added to the program, bespoke is possible but within some boundaries.
In conclusion - none of the methods listed above is right or wrong, it depends what outcome you want
As a result of this informal discussion my friend now knows more and can make a better-informed decision in the future. His company also has clear goals / steps in their 5-year plan as to where they would like to be as the business expands. My friend knows Symetri, as a trusted advisor, will always be here to ask questions and give answers to help him grow his business.
It is good to talk to someone at Symetri about your Bill of Material needs. Your success is our success, we challenge you to work smarter for a better future.
You can also contact myself at any time.
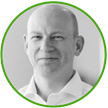
Tim Ray
Sovelia Product Manager