It’s no secret that the essential role of product lifecycle management (PLM) is to inform or put the right information into the right hands at the right time. Any professional involved in a product’s development or manufacture, any organisation that sells a product or has customers who uses it, or procurement who specify and purchases it, they all need information to assist and drive their involvement with the product and ultimately a products success.
What is sometimes less well understood, is how to capture the information and present it in a format everybody can work with, contribute to where appropriate, and share. If a company has very little or intermittent collaboration today, by adding a PLM software solution it enables more people to share more information, in a meaningful way.
Has your organisation got answers to these questions and secure, automated processes to support them?
-
How is the Engineering or Design department communicating with the rest of the organisation?
-
Who do Engineers or Designers need information from and who do they need to send information to?
-
Which other departments do they interact with? How is that information captured?
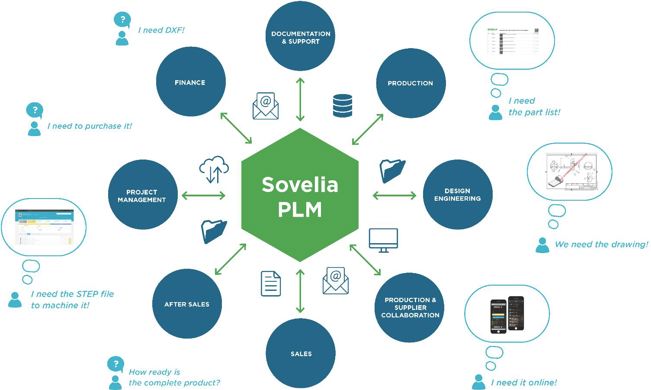
Image: Sovelia PLM supporting collaboration and securing correct product information across the business.
Example of areas where Sovelia Core for PLM helps to be more collaborative:
- Access to the right information at the right time
- Access globally anytime
- Intuitive HTML user interface for all users
- Personalised view of the information
- Role-based access
- Approval processes
- Supporting document generated automatically
Sovelia Core
Helps your company to grow
...and grows with your company.